マシニングセンタ加工の流れ
当社では、以下のようにマシニングセンタで加工準備・加工を行います。
1. 工具、条件を決めるために
1. 加工材料、加工形状の確認
加工材料の材質(鉄、アルミなどの組成)、硬度、図面から加工形状を確認し、使用する工具の径や形状をおおまかに決めます。当社ではマシニングセンタで様々な材質、形状の加工に対応するために主に以下の種類の工具を使用しております。下記以外の工具を使用しなければならない場合には、別途工具を取り揃え加工しています。
工具の形状 | 工具径 | 工具の特徴 | 工具の材質 |
---|---|---|---|
ボールエンドミル | R0.03~3 | 先端が球状で主に曲面の加工に使われる。 | 超硬合金、CBN、PCD、電着 |
スクエアエンドミル | φ0.1~6 | 先端が平坦な形状で水平面や垂直面を切削加工するのに使われる。 | 超硬合金、CBN、PCD、電着 |
ラジアスエンドミル | φ0.3~6 | スクエアエンドミルの角に丸みがある形状で、ボールとスクエアの中間的なエンドミル | 超硬合金、CBN、PCD、電着 |
ドリル | φ0.05~3 | 穴あけ加工に使われる。 | 超硬合金、CBN、PCD、電着 |
超硬合金
炭化タングステン(WC)に靭性の高いコバルト(Co)をバインダーとして成型・焼結し作られます。切削用超硬合金は、刃先を高温度で強度を上げ、さらに炭化チタン(TiC)、炭化タンタル(TaC)などの高融点金属を加えさらに強度を上げている。最近はセラミックス系やダイヤモンドなどのコーティングを施した超硬合金が作られています。
CBN(Cubic Boron Nitride)
ダイヤモンドに次ぐ硬さを持つ素材で、鉄系材料との反応性が小さく、ダイヤモンドより熱化学的に安定性に優れています。そのため、鉄系材料を加工する際にはダイヤモンドよりCBNを用います。最近ではCBN径の微細化やバインダーの改良により、一般炭素鋼や焼入れ鋼の加工においても大きな効果を示すようになってきています。
PCD(Poly Crystalline Diamond)
多結晶焼結ダイヤモンドのことで、天然ダイヤモンドに次ぐ硬度を持ち、耐摩耗性に優れ、超硬合金工具に比べて飛躍的に長寿命であり、靭性が高く非鉄金属加工でも重切削ができることや構成刃先が付きにくいことから高品位・高精度加工に効果的です。
電着
母材上にダイヤモンドもしくはCBN粒子をニッケルメッキで単層固定した工具です。セラミックスや超硬合金、焼入れした鉄系金属などの難削材を高効率・高精度に加工することができます。母材の形状を複雑にすることで、複雑形状の加工が可能となります。母材の形状が変形していなければ、再利用が可能です。
上記の工具から加工条件に最適な工具を選択し、加工します。
2. 最終的な加工形状から逆算して加工順序・条件を選択しプログラム作成
最終図面から逆算して加工順序・条件(使用工具の順番、回転数、送り速度、切削速度、切削方向、切削油の選択など)を考え、プログラムを作成します。
回転数
回転数は、1分間あたりの主軸の回転数のことで、min-1で表されます。回転数は加工材質や工具長、工具径によって左右され、一般的には削りにくい材料や太い工具径、工具長の長い場合ほど、回転数を遅くします。回転数が早いほど加工時間を短縮することができます。当社には50000回転までの主軸回転能力を持つマシニングセンタがあります。また専用のエアスピンドルを着用することで150000回転の加工を行うことができ、最新の設備が整っています。
送り速度
機械のテーブルと主軸(工具を回転させる)の1分間あたりの移動量のことで、mm/minで一般的に表されます。送り速度の増加は、切削抵抗の増加、加工面粗さの低下、工具磨耗量の低下などの影響がみられます。送り速度が過剰に速いと加工精度の悪化や加工変質層の発生などの影響が生じ、逆に過小な送り速度の場合、加工能率の低下、工具寿命の低下などの影響が生じます。送り速度は機械剛性と工具剛性(材質特性を含む)、要求される加工精度によって決める必要があります。
切削速度
切削速度は、主軸回転数×工具の直径×π÷1000で表されます。切削速度が遅いとせん断角度は低く、切りくずの厚さが厚くなり、速いとせん断角度が高くなり、切りくずの厚さは薄くなります。切削速度の増加は加工面粗さが向上、切削抵抗性増加の抑制、工具の短寿命化(耐熱性の改善された工具の場合には工具寿命の延長)、工具の振動の増加などの影響がみられます。切削速度は加工能率や加工面の品位向上の面からできるだけ速い方がいいですが、工具の寿命や振動などを考慮し、切削速度を決める必要があります。
切削方向
切削方向にはアップカットとダウンカットがあり、それぞれ図に示します。アップカットは刃が加工材料を掬い上げながら加工していく方法で、ダウンカットは加工材料に噛み込みながら加工していく方法です。アップカットは加工材料への刃先の切り込みがゼロから始まり次第に厚くなり、主に微小切り込みの仕上げに用いると効果的で、刃先のこすりにより逃げ面の工具磨耗が早いが、食い付き時の衝撃が小さいので工具はカケにくくなります。またバリ(金属のササクレ)、加工材料の硬化(刃先のこすりにより)が生じやすくなります。それに対してダウンカットは刃先の切り込みが次第に薄くなっていき、逃げ面の機械的こすり磨耗が緩やかになる傾向があり、工具寿命がアップカットに比べて長くなり、その反面食い付き時の衝撃により突発的な工具のカケが生じやすくなります。加工材料にはバリが生じにくくなります。
切削油
一般的には加工中に切削油を加工部位にかけながら加工を行います。切削油の効果として、潤滑効果、冷却効果、切りくずの排出効果などがあります。潤滑効果として工具磨耗、切削抵抗、発熱量の減少、工具と切りくずの凝着の防止があげられます。冷却効果としては、熱膨張を減らして寸法精度の低下を防止したり、刃先の温度を下げて刃先の軟化を防ぎ、工具寿命の延長をもたらします。発熱と急冷却を繰り返すことで大きな熱応力が生じ、サーマルクラック(熱亀裂)を発生させたり、加工材料によっては刃先温度を下げたために構成刃先(加工材の一部が刃先に付着し、それが成長し新たな刃として振舞うことで、いずれ切削力に耐えられなくなり脱落します。)を発生させ、加工面粗さを悪化させることがあります。その問題に対応するために、冷却効果を伴わず潤滑効果だけを高めるMQL(Minimum Quantity Lubrication)と呼ばれる超微量の切削油剤をエアに混合しミスト状にして供給する方法があります。さらに過冷却の状態をもたらさず切りくずの強制排出を行いたい場合には、エアブローでの対応も効果的です。
当社では、今までの加工実績や実験で得たノウハウから加工材料に最適な加工条件を熟練のオペレーターが判断し、加工順序・条件をプログラミングします。
2. 工具準備
工具をマシニングセンタにセッティングするのに、焼きばめという作業を行います。焼きばめとは、熱膨張と収縮を利用し2つの物質を結合させる方法で、工具をマシニングセンタにセッティングする場合には、工具とシャンクと呼ばれる工具を固定する器具を用います。
- 1. 焼きばめを行う装置でシャンクを加熱し、シャンクの内径を熱膨張により広げます。
- 2. 広がったシャンクの内径に使用する工具をはめこみます。
- 3. 工具をはめこんだら冷却し、シャンクの内径を収縮させ工具をシャンクに固定します。
焼きばめで工具をセッティングすることで高精度・高信頼性・作業の簡素化、工具寿命の延長、高精度加工のメリットがあります。
高精度・高信頼性
従来用いられていた手締めで工具を固定するコレットチャック式に比べて、構成部品が最小で高剛性、高精度な工具固定が可能です。繰り返し使用しても精度が高いので、セッティング後の確認作業が不要で、また作業の簡素化によりセッティング作業の習熟度も不要となります。
工具寿命の延長
高精度の工具のブレ制御、高剛性の保持により、工具寿命の安定化と延長が期待できます。
高精度加工
加工中の高速回転による工具のブレを数μm程度で制御できるので、高精度の加工が実現できます。
150000回転の加工を行う場合にはエアスピンドルを用いるため、機械の構造上焼きばめを行うことができません。そのため専用の手締めのコレットチャックを用い、工具を固定します。工具の計測を行う際に、レーザー測長機ブルームで主軸のズレを計測し補正を行って加工します。
3. プログラムのシミュレーション、在庫の確認
作成したプログラムをパソコン上でシミュレーションし、図面通りの加工ができるか確認します。確認できたら、在庫の工具本数、形状を確認し、足りない場合は注文します。工具は1度使用すると刃の先端に磨耗やカケが生じることがあり、磨耗やカケに気づかずに加工した場合、加工後に顕微鏡で確認した時に加工できていないことがあるので、工具形状を顕微鏡で確認することはマシニングセンタへ工具をセッティングする前に必ず行います。マシニングセンタには10本ほど工具を格納しておくことができるので、確認した工具はマシニングセンタに格納しておきます。加工精度によっては工具径の計測をマシニングセンタ付属のレーザー測長機ブルームで測定します。30μmの工具径からブルームで計測可能で、ミクロンオーダーでの精度が求められる場合には使用します。
4. 材料のセッティング
マシニングセンタに冶具をセッティングします。冶具とは加工材料を固定するとともに切削工具の制御、案内をする装置のことです。加工材料によりますが、加工材料を載せる土台となるマグネット式の冶具やバキューム式の冶具をマシニングセンタにセッティングします。セッティングした後は冶具表面の平坦度をダイヤルゲージで計測します。平坦度が保たれていない状態で加工すると、加工した場所により深さに違いが生じ、ミクロンオーダーの加工に対応できません。土台となる冶具の平坦度が保たれていないと、セッティングする加工材料も平坦度を保てないので慎重にセッティングします。冶具の平坦度が確認できたら、加工材料を載せ同様に平坦度、平行度を確認しながら冶具で固定します。
5. 材料の原点出し
マシニングセンタの加工範囲内には機械座標と呼ばれるマシニングセンタ内の絶対座標がX軸、Y軸、Z軸にそれぞれあり、この座標範囲内でプログラムの指示した座標地点を加工することになります。
冶具にセッティングした加工材料をスタイラスと呼ばれる高精度計測器で測定する(加工材料が直方体なら4点)ことで、加工材料の中心を測定することができます。この中心を原点としてプログラムを実行します。
スタイラスは工具と同じようにマシニングセンタにセッティングし、加工材料の中心出し、加工材料側面からの位置決め、内径・外径測定、2点の位相位置などを測定することができます。
スタイラスや工具を同じ座標に移動させるようプログラムを組んでも、誤差が生じます。これはマシニングセンタの性能によって違いますが、当社にあるマシニングセンタでは位置決め精度±0.25~0.3μm、繰り返し精度±0.1μmと非常に高精度で位置決め・測定を行うことができます。
6. 工具の計測
上記の準備ができたらプログラムの読み込みを行います。加工前の工具交換時には工具径と工具長を、加工後の工具交換時には工具長を計測するようになっています。
工具の計測はブルームで行い、計測前に20分程度使用する回転数で慣らし運転してから計測します。工具は1分間あたり1000回転単位の高速回転を行うと熱を生じミクロンオーダーで伸張が見られるため、慣らし運転を行います。
伸張した状態の工具で加工を行わないと、途中で工具の伸張が生じて、工具が破損したり、狙い通りの加工ができないことがあります。加工前にブルームで計測した工具径で補正をかけ、狙い通りの加工ができるようにします。
加工後に工具長を計測するのは、加工中に工具が磨耗していないか確認するためで、磨耗していると狙い通りの加工ができていない場合があります。レーザー測長機では工具の計測以外に高速回転主軸の位置ズレを0.1μm単位で補正することができます。
7. プログラムの実行
工具の計測が終わったらプログラムに従って自動で加工が行われます。基本的には下のような順序でプログラムを組み、加工を行っていきます。加工するものによっては20時間以上かかる場合もありますが、自動加工なので夜間も加工を行うことができ、人がずっと付きっ切りでいる必要はありません。
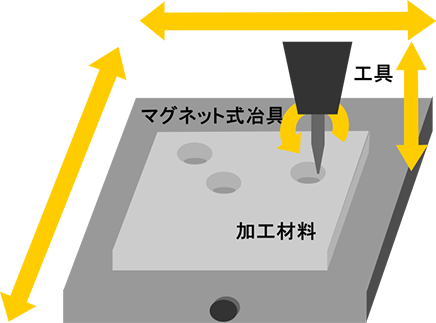
基本的な切削加工順
粗取り
径の大きな切削工具で大まかな形状の加工
↓
中仕上げ
径の小さい切削工具で微細な加工
↓
最終仕上げ
径の小さな切削工具で加工箇所をなめて滑らかな加工面に仕上げる
径の小さな切削工具を使用する時ほど回転数を上げ、送り速度を遅くする。